Blog Navigation: Business Insights and Spotlights | Chamber Blog
07.22.25
How John Deere Fargo is Building Tomorrow’s Workforce
By Tyler Fischbach, Vice President of Public Relations, The Chamber
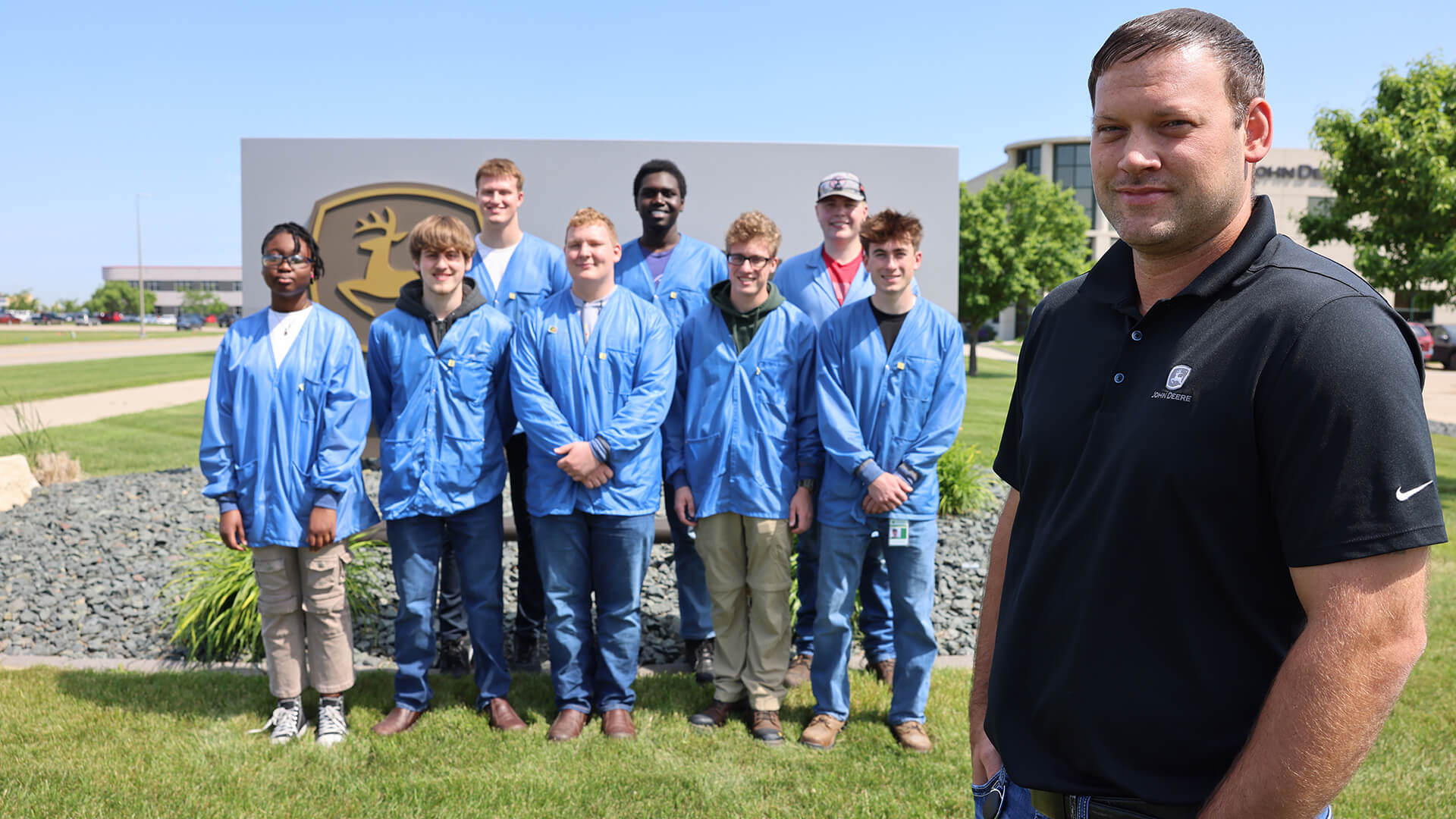
Jameson Benson, Engineering Supervisor at John Deere Intelligent Solutions Group, with several John Deere apprentices in Fargo, North Dakota.
When Jameson Benson started recruiting for John Deere's new apprenticeship program in Fargo, he faced an unusual challenge: he didn't know any high school students. As an engineering supervisor with 13 years at the company, he'd mastered complex manufacturing processes and product development. But convincing 16-year-olds to choose industrial electronics over traditional after-school jobs? That was uncharted territory.Â
Nearly three years later, what started with Brody Kessler — a single apprentice with a passion for STEM — has evolved into a comprehensive program that's transforming how John Deere Fargo builds its technical workforce. The program is expanding, attracting attention from leadership across the company, and most importantly, changing the trajectory of young people's careers before they even graduate high school.Â
"We're looking at students who could graduate college with six to seven years of relevant John Deere experience," Benson explains. "Imagine the power that provides."
From Challenges to Innovation
Like many manufacturers, John Deere faced a critical question: How do we fill our talent pipeline? Engineering Manager Kelly Hagel saw the gap clearly. While Deere had built a strong engineering pipeline through years of partnership with North Dakota State University (NDSU), they had nothing similar for technicians.Â
"On the engineering side, we've had a really strong part-time student program for many years," Hagel explains. "When I looked at the technician side of things, we didn't have any sort of pipeline. We didn't have any plan at all."Â
After connecting with other John Deere locations running successful welding apprenticeships across the country and partnering with the North Dakota Department of Labor and area school systems, Hagel launched an initiative tailored to Fargo's unique needs. Hagel brought in Benson to execute the vision, as his hiring coincided perfectly with the program's launch.
Starting From Scratch
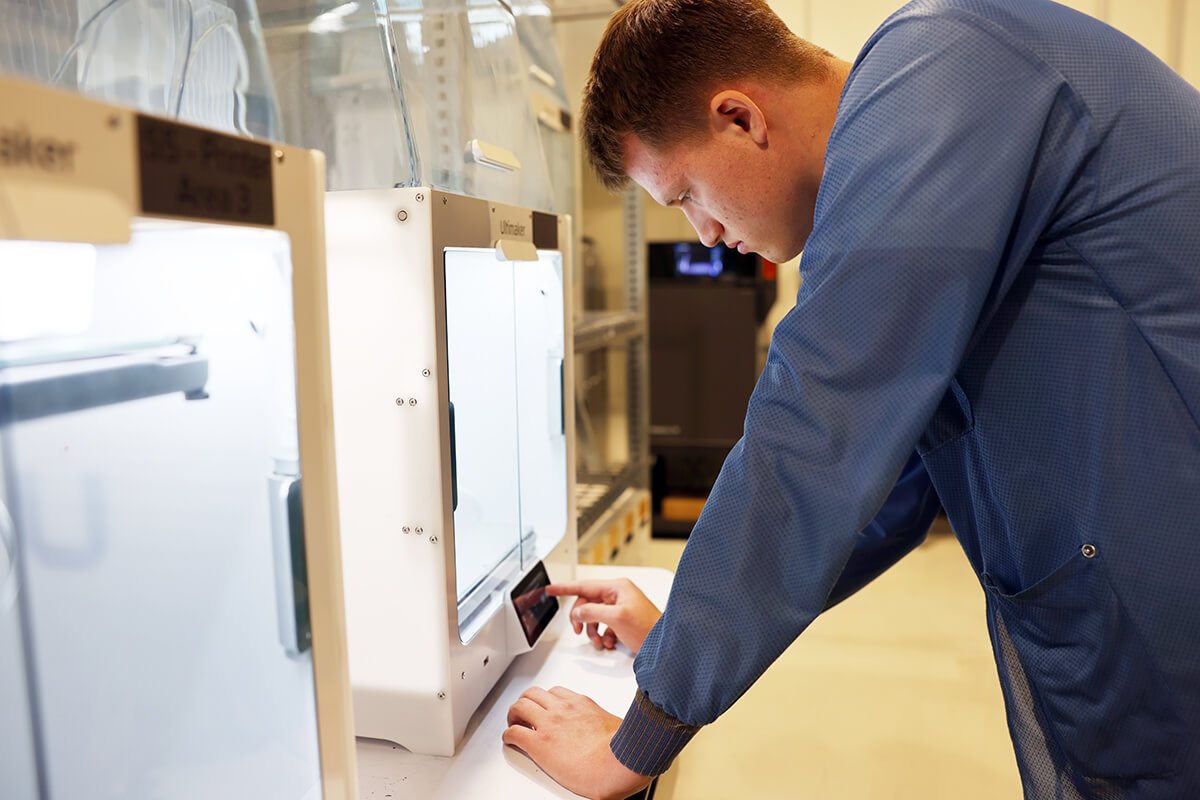
John Deere's very first technician apprentice, Brody Kessler, operates a 3D printer.
Creating an apprenticeship program meant challenging company norms. "Our company policy is that you have to be 18 years old to work here at any level," Benson recalls. "So how do we start analyzing and updating that, and other policies we have?"Â
Next, the team had to define exactly what skills technicians needed for long-term success, then build training programs from scratch. Their first year, they brought on a single apprentice and learned constantly.Â
"We have a 'lessons learned' document every year," Benson says. "We update this each year with things that didn't go well, and other things that went great."Â
The program's structure emerged through trial and refinement: students join after their junior year of high school, working full-time that first summer. This intensive start is crucial in their technical field.Â
"If you start during the school year working 10 hours a week, it's very difficult to get up to speed to where you're actually able to do something on your own," Benson explains. After that foundational summer, students work part-time during their senior year, then return full-time after graduation.Â
The High Performer Connection
Recent research at John Deere revealed a powerful correlation: employees who receive early structured training are significantly more likely to become high performers later in their careers. This finding has reshaped how the company thinks about talent development.Â
For Brody, the connection between hands-on work and academic learning has been transformative.
"I've been doing a lot of 3D modeling and printing. I've learned skills like soldering and making wire harnesses," he explains. "A lot of that's translated over to what I do in school—physics, center of mass, electrostatics. I've been able to apply what I've learned here to my education."Â
This practical application helps students see problems differently. "They tell me what they need done, and then there are a million ways to do it," Brody says. "You just got to figure out what the best one is. A lot of trial and error, but it's like a puzzle."Â
When new graduates join the workforce, they often feel pressure to immediately solve any problem placed before them. John Deere recognizes this tendency and takes a unique approach with all of their new talent.Â
"We have to reassure them that the expectation is not that they know how to do everything right away," Benson says. "It's important not to try to train on the entire problem all at once. There are all these little pieces. Train on those individual pieces, and over the years, they'll get there."Â
The Ripple Effect
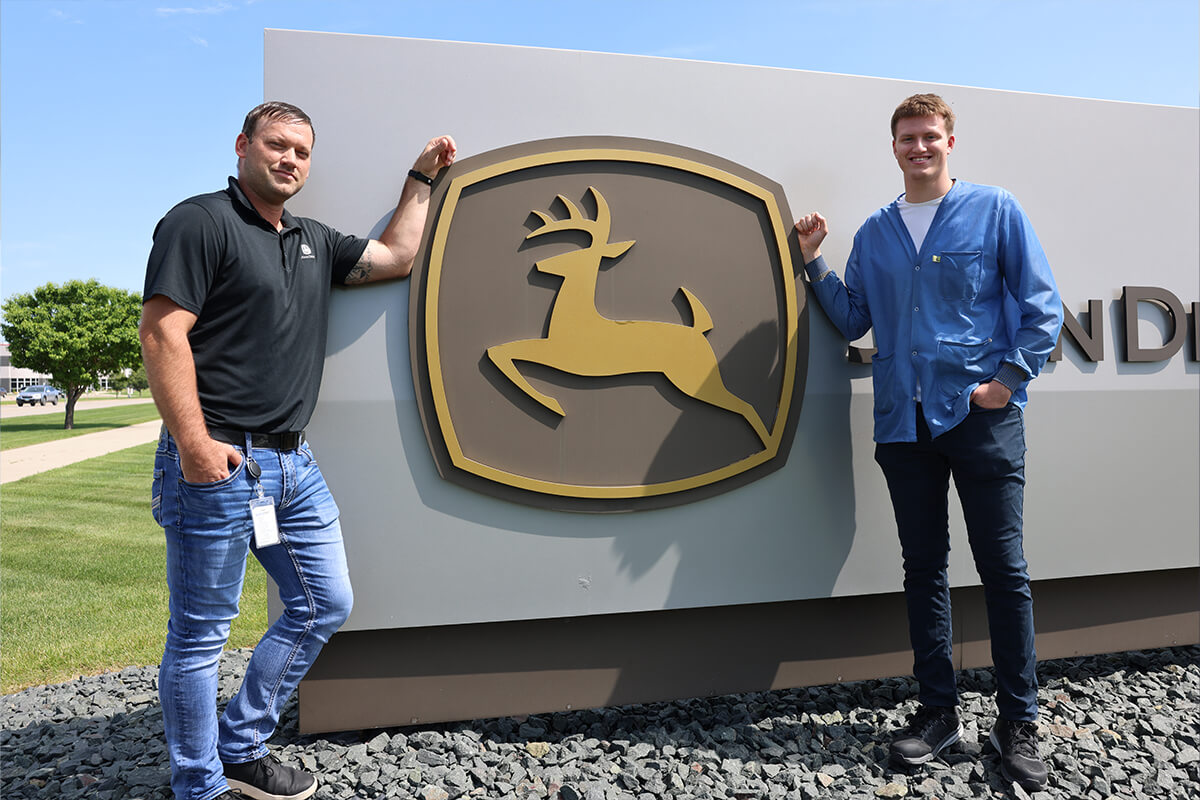
Jameson Benson and Brody Kessler outside of the John Deere facility in Fargo, North Dakota
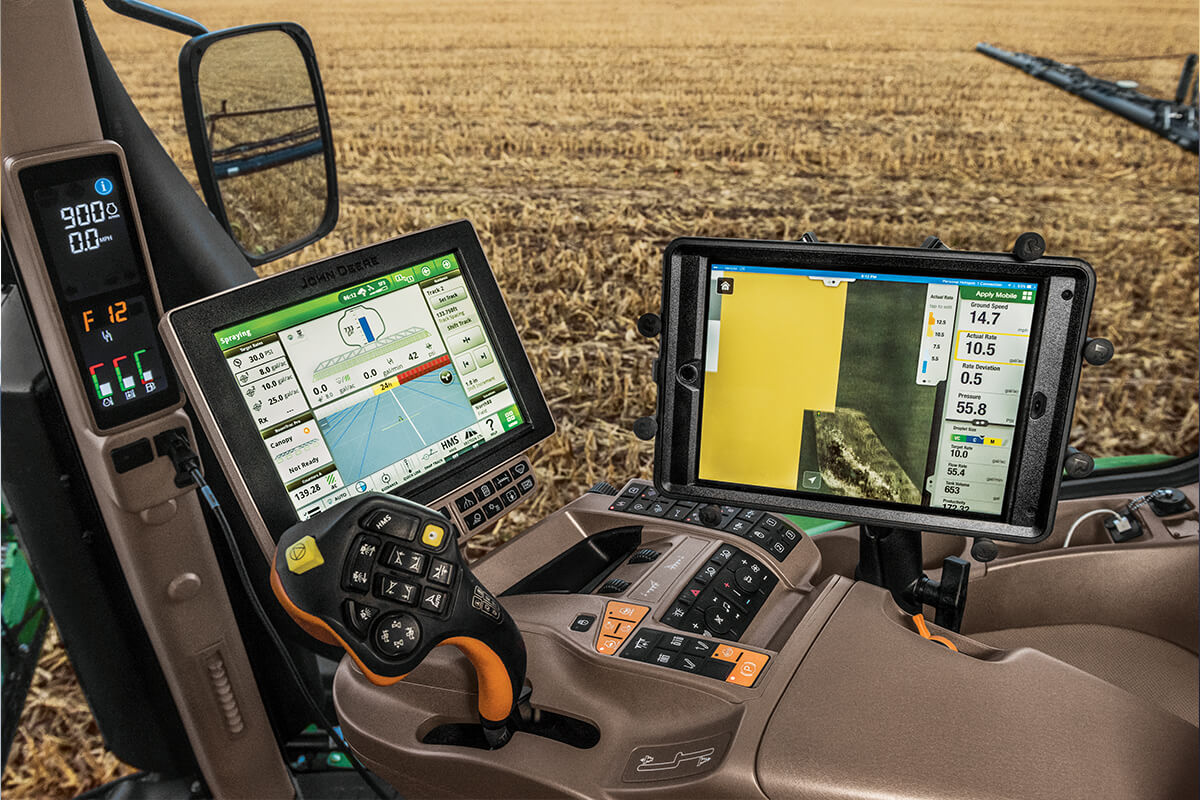
Technology developed by the Intelligent Solutions Group on display inside the cab of a John Deere tractor.
For the broader community working to address workforce challenges, John Deere's model offers a blueprint: identify your specific needs, start small, learn constantly and don't be afraid to challenge traditional approaches. There must also be a willingness to invest in long-term development over quick fixes.Â
For Benson, who once wondered how to connect with high school students, the transformation has been remarkable. From that single apprentice in year one to a growing program attracting corporate attention, the journey demonstrates what's possible when companies commit to building their own talent pipelines.Â
His advice to businesses on the cusp of starting similar programs is simple: "Just start. Start asking questions, start testing, start getting the ball rolling."Â
In an era when many companies struggle to find skilled workers, John Deere Fargo isn't waiting for talent to arrive—they're creating it, one apprentice at a time.Â
Read the full story in The Bridge
SHARE
More Stories
Upcoming Events
Subscribe to email newsletters